Home
AUGUSTAIR
SERVICE BULLETIN SB2009-1
Revision B
Initial Release Date: 3 November 2009
Revision A Date: 15 January 2010
Revision B Date: 2 February 2010
Subject: Vertical Stabilizer Spar Inspection, Repair
and Reinforcement.
SECTION 1. Planning Information
A. Effectivity:
(1) Morrisey 2150, Shinn 2150A, Varga 2150A,
Varga 2150 ATG, Varga 2180 and Varga 2180TG
B. Reason
(1) Cracked or broken vertical stabilizer
front spar and/or loose or missing fasteners at the bend in the spar
where it attaches to the fuselage FS 193.06 bulkhead (See Figures 1, 2
and 3) due to Metal Fatigue caused by repeated operational loads. The
spar flanges are notched to facilitate the bend. The notches are
spanned by splice straps. These detail design features of the spar
bend design (including tolerances) induce stress concentrations due to
the interaction of the flange notch and the flange bend radius that
may not be entirely mitigated by the splice straps.
(2) Cracks may occur at or near the flange
notch root propagating across the spar web or up the flange bend
radius. In addition, redistribution of internal loads due to a cracked
or broken spar may cause fasteners attaching the splice straps to
loosen.
C. Description
Augustair recommends a detailed visual and dye-penetrant
inspection of the front spar near the bend, and incorporation of a spar
web doubler either as a repair or as a preventative alteration in
accordance with the instructions in Section 2 of this Service Bulletin
unless the inspection and repair or alteration incorporating the spar web
doubler described in Section 2.B. has already been accomplished and
approved by the FAA.
(1) Preliminary Inspection for security and
condition of the vertical stabilizer attachment in accordance with
Section 2.A.
a. If the preliminary inspection indicates
damage or looseness, then accomplish the Detail Inspection and Repair
or Alteration in accordance with Section 2.B. before further flight.
b. If the preliminary inspection does not
reveal damage or looseness, then accomplish the Detail Inspection and
Repair or alteration in accordance with Section 2.B. within 10 hours
time in service from the time of the preliminary inspection.
Note
: The preliminary inspection is
insufficient to find and repair all fatigue cracks in this area. If
the vertical stabilizer is damaged to the extent that it is noticeably
loose in the preliminary inspection, then further flight, even a ferry
flight, is strongly discouraged. If no damage is evident in the
preliminary inspection, then a ferry flight or normal operations for a
very short time (up to 10 hours time in service) is permissible. The
preliminary inspection may be omitted if the detail inspection and
repair / alteration is done immediately.
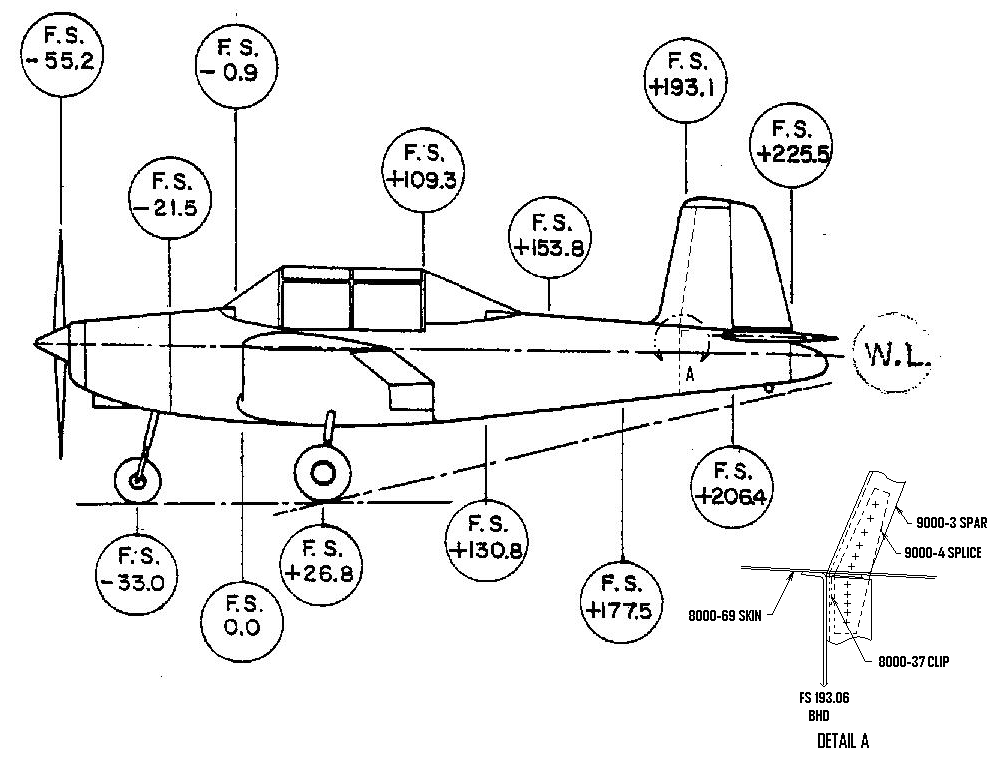
Figure 1
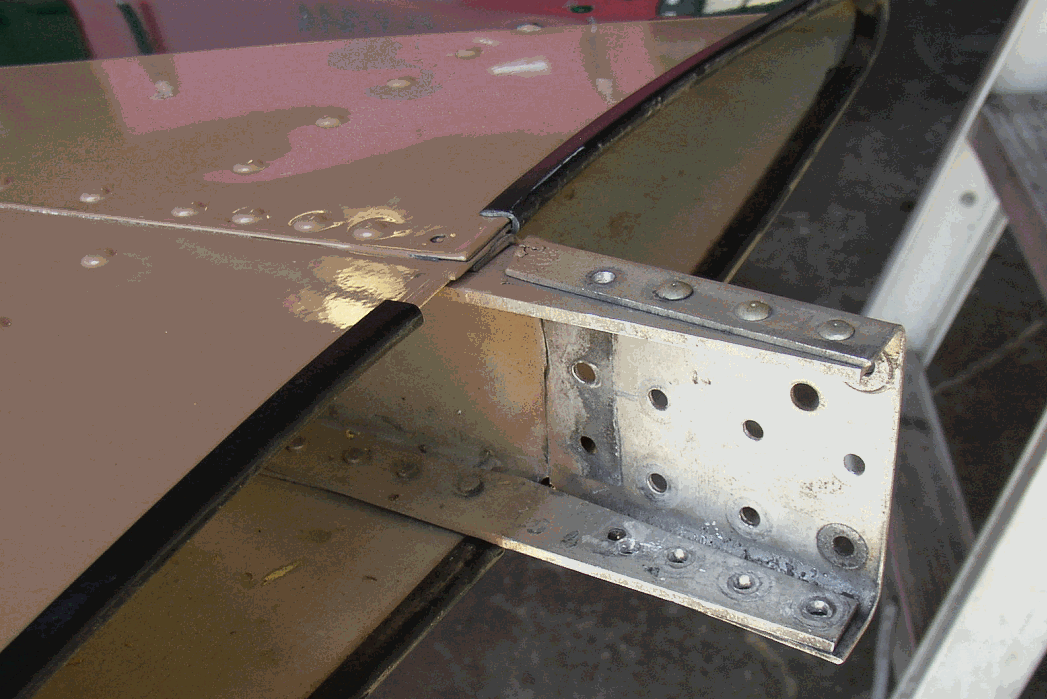
Figure 2
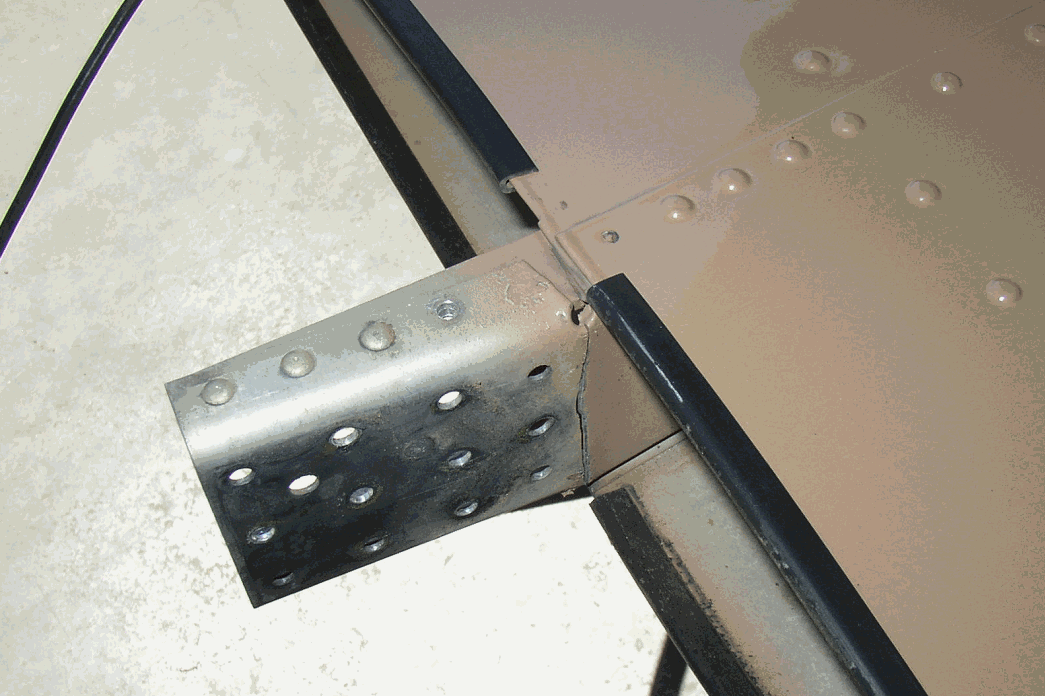
Figure 3
D. APPROVAL
The EFFECTIVITY information in Section 1.A(1) and
the technical content of ACCOMPLISHMENT INSTRUCTIONS of Section 2. of this
service bulletin are FAA approved.
E.COST
Estimated costs for implementing the inspections
and repairs or alterations are:
Workhours
Materials
(1) Preliminary Inspection
1.0
Σ 1.0
(2) Detail Inspection and Repair or Alteration
a. Remove Vertical Tail 2.75
b. Inspect 1.0 dye penetrant
c. Fabricate and Install Doubler 2.0 0.090 clad
2024
2024-T3 al alloy
Corrosion preventative finish
d. Reinstall removed structure 7.0 miscellaneous
e. Checks and reinstall access
1.5
Σ 14.25
F. CORRESPONDENCE
(1) Augustair, Inc.
1809 Heph. McBn. Rd.
Hephzibah, GA 30815
(2) Varga type club: The VG21 Squadron
http://VG21squadron.com
SECTION 2. Accomplishment Instructions
A. PRELIMINARY INSPECTION
(1) Before further flight unless an approved
repair/alteration consistent with the installation of the repair or
alteration doubler in Section 2.B has already been accomplished, or if
the Detail Inspection and Repair or Alteration in Section 2.B is elected
to be accomplished before further flight.
(2) Hand Check Security of Vertical Tail
a. With the airplane parked and secured, push
by hand laterally to the left and to the right on the vertical tail at
least 1 foot above the fuselage with sufficient force to rock the
airplane slightly to moderately.
b. If any evidence of looseness or relative
motion between the vertical tail and the fuselage is observed, then
proceed to Detail Inspection and Repair or Alteration in Section 2.B.
before further flight.
c. If no evidence of looseness or relative
motion between the vertical tail and the fuselage is apparent, then
perform Visual Inspections in Section 2.A.(3).
(3) Visually Inspect the Vertical Tail Front
Spar at Fuselage Penetration
a. Access through vertical stabilizer seal
i. Temporarily remove/dislodge the
rubber/plastic seal at the base of the vertical tail sufficiently to
visually inspect the vertical tail front spar at the intersection
with the fuselage.
ii. Using a flashlight and other aids as
appropriate, visually inspect for cracks in the spar web and splice
plates and for loose, missing or otherwise damaged fasteners.
Figures 2 and 3 above depict the area to be inspected (after tail
removal and cleanup). With the seal partially removed some of this
region may be sufficiently visible if paint over-spray and sealant
permit.
iii. If damage is detected or if sealant or
paint overspray obscures the area so as to prevent close visual
inspection, then proceed to Detail Inspection and repair or
Alteration in Section 2.B. before further flight.
iv. If sealant and/or paint overspray does
not obscure the area and a close visual inspection does not reveal
damage, then proceed to 2.B.(3)b. visual inspection with access
through the Rudder/Elevator Access Panel.
b. Access through the Rudder/Elevator Access
Panel
i. Remove the access panel on the fuselage
side panel (Figure 4, Item 17).
ii. Visually inspect areas at the
attachment of the vertical tail forward spar to the FS 193.06
bulkhead for cracks, loose or missing fasteners, evidence of
chaffing or relative movement and corrosion using a flashlight (and
mirrors as required). A boroscope, or other magnifier, or other aids
may optionally be used.
iii. If damage or severe corrosion is
detected or if sealant or paint overspray obscures the area so as to
prevent close visual inspection, then proceed to Detail Inspection
and Repair or Alteration in Section 2.B. before further flight.
iv. If damage is not revealed and corrosion
is mild, moderate or none, then optionally:
(1) Proceed to Detail Inspection and Repair
or Alteration in Section 2.B, or
(2) Replace the access panel and
rubber/plastic seal at the base of the vertical tail and perform
Detail Inspection and Repair or Alteration in Section 2.b. within 10
hours time in service after this inspection.
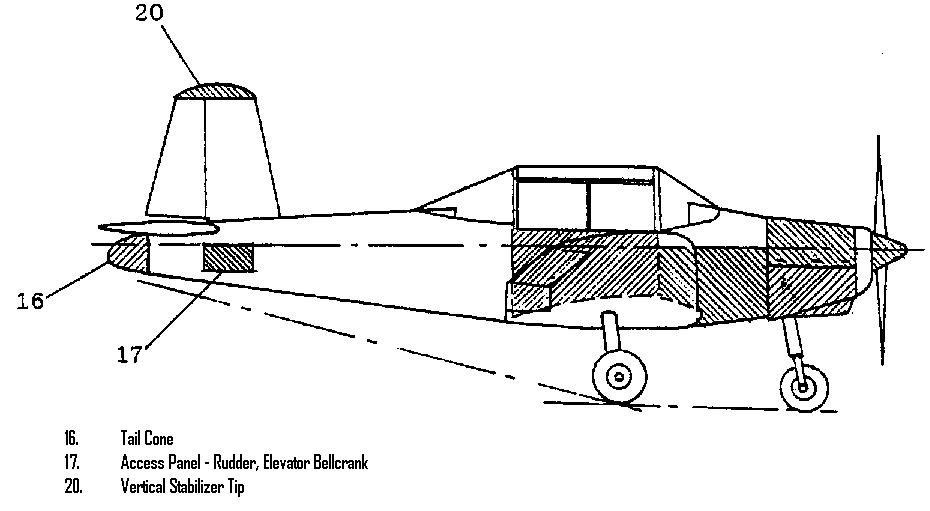
Figure 4
B. DETAIL INSPECTION AND REPAIR OR ALTERATION
(1) Unless
a. the inspections describe below have
already been accomplished and the repair / preventative modification
(alteration) doubler described below has been installed or
b. an approved repair or alteration
accomplishing the intent this Service Bulletin has been installed:
If the Preliminary Visual inspection in
Section 2.A reveals damage or is optionally skipped, then before
further flight perform the close visual and dye-penetrant inspections
and fabricate and install a spar web repair or preventative
modification doubler as described below before further flight.
If the Preliminary Visual Inspection in
Section 2.A is performed and does not reveal damage, then perform the
close visual and dye-penetrant inspections and fabricate and install a
spar web repair or preventative modification doubler as described
below within 10 hours time in service after the Preliminary
Inspection.
(2) Remove the Vertical Stabilizer:
Note: Vertical Stabilizer removal and
installation is addressed in the Varga Kachina 2150A Aircraft
Maintenance Manual Section 4.4.4.1 which may be used to supplement
the following instructions.
Note: The Maintenance Manual paragraph
4.4.4.1 vertical stabilizer removal requires removing the rudder in
accordance with paragraph 4.4.3.1, which requires removing the
horizontal stabilizer in accordance with paragraph 4.4.2.1, which
requires removing the elevator in accordance with paragraph 4.4.1.1.
However, the elevator and horizontal tail may be removed as an
assembly after disconnecting the controls in accordance with the
instructions below.
a. Gain Access, Remove the Tailcone,
Disconnect Controls and Optionally Remove the Elevator:
i. Remove the access panel from fuselage
right hand side (Figure 4, Item 17).
ii. Remove the fiberglass tail cone (Figure
4, Item 16) disconnecting the tail light wire at the knife splice
(Figure 5).
iii. Remove two AN3 bolts attaching the
elevator horn to control tube connection (Figure 6)
iv. Disconnect the rudder cables from the
rudder bell-crank (Figure 7) two places. Temporarily replace the
hardware in the bell-crank to avoid loss of the bushings (figure 7,
Item 7)
v. Remove the 2 AN3 bolts attaching the
elevator static balance weights to the elevator bell-crank, remove
the weight assemblies. (Figure 6).
vi. Optionally, for ease of rudder removal,
remove 2 AN3 bolts attaching the rudder static balance weight from
the horn (Figure 7), remove the weight.
vii. Optionally, support the elevator,
remove 3 AN3 hinge bolts and remove the elevator.
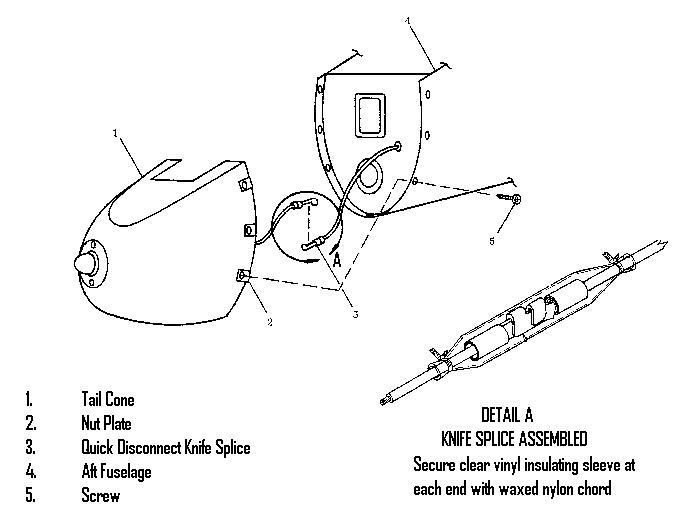
Figure 5
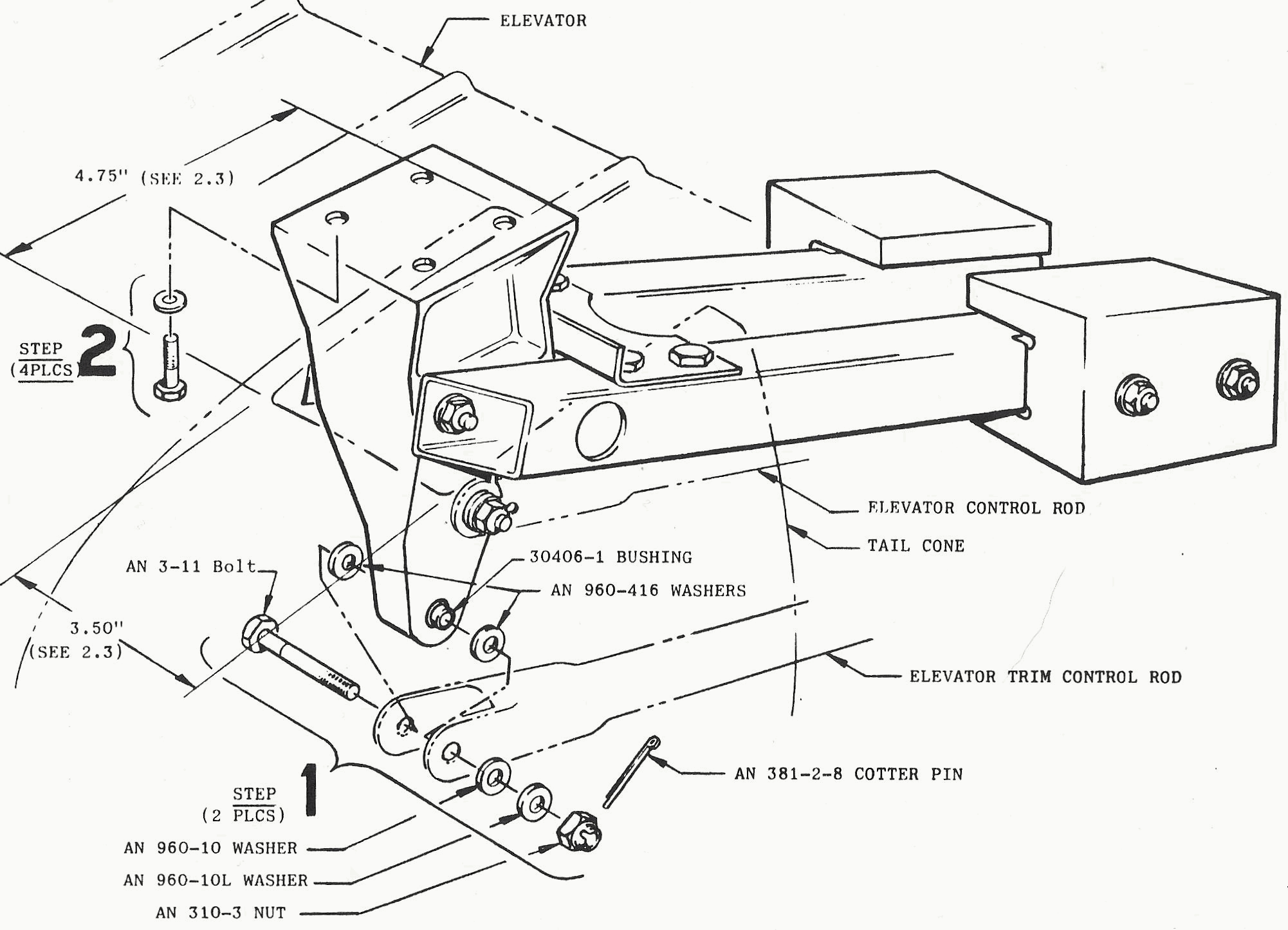
Figure 6
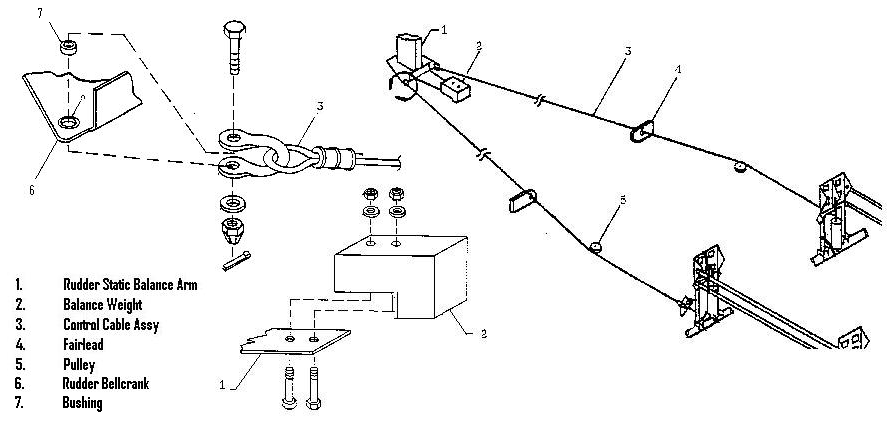
Figure 7
b. Remove the Horizontal Stabilizer
i. Remove the horizontal stabilizer attach
hardware at 4 locations on the underside of the stabilizer (Figure
8).
ii. Support and remove the stabilizer (or
the stabilizer and elevator as an assembly if the elevator was not
removed in step a.) by lifting up and sliding aft.
iii. After moving the stabilizer to clear
attachment angles, temporarily re-insert the bolts to retain the
fixed spacers between the stabilizer surfaces (Figure 8, Item 9).
iv. If the Tail Light wire impedes removal,
it is permissible to cut the wire.
Figure 8
c. Remove the Rudder:
i. Remove the Vertical Stabilizer Tip.
ii. Support the rudder, remove the hinge
bolts (2 hinges) and remove the rudder.
d. Remove the Vertical Stabilizer
i. Disconnect the VOR Antenna cable if
installed. It is permissible to cut the cable.
ii. Support the vertical stabilizer and
remove the fasteners attaching the vertical stabilizer front spar to
the FS 193.06 bulkhead (Figure 9). In some models these are 12 NAS
1103-3 bolts. In others they are rivets. If rivets are installed,
then carefully drill-out rivets using guidance in AC 43.13-1B,
paragraph 4-52.b.
iii. To facilitate removal of the vertical
tail, the 8000-37 clip (Figure 9, Item 11) attaching between the
spar and the 8000-69 fuselage skin at the top of the FS 193.06
bulkhead may be optionally removed at this point. Carefully drill
out the 3 AN470 rivets attaching the clip to the skin and remove the
clip.
iv. Remove fasteners attaching the vertical
stabilizer aft spar to the FS 206.38 fuselage bulkhead and to the
8000-8 horizontal bulkhead (Figure 9). On some models these are 6
NAS 1103-3 bolts (spar to FS 206.38 bulkhead) and 4 NAS 1103-2 (spar
to the 8000-8 horizontal bulkhead). On others these are rivets. If
rivets are installed, then carefully drill-out rivets using guidance
in AC 43.13-1B, paragraph 4-52.b.
v. Attachment bolts are different lengths,
mark them for re-installation. Subsequent installation of a front
spar web doubler will require longer bolts for attaching the front
spar to the FS 193.06 bulkhead.
vi. If the Tail Light wire impedes removal,
it is permissible to cut the wire.
vii. Remove the vertical tail lifting
straight up to clear fuselage slots and attachments.
viii. Some airplanes may have an optional
tapered shim installed between the vertical stabilizer front spar
and the FS 193.06 bulkhead. If one is installed retain it for
subsequent reassembly, or if damaged, fabricate a new one using the
existing one as a template (see reassembly, below).
Figure 9
(3). Remove excess paint and clean the areas
near the bend in the 9000-3 vertical stabilizer front spar at least 3.0
inches above the bend and to end of part below the bend including the
9000-4 splice plates (Figures 1, 2, and 3) using shop solvents per AC
43.13-1B Chapter 5, Section 5 Table 5-5 as required to prepare the area
for inspection in accordance with the inspection method below. Exercise
caution so as to not damage the structure or finishes more than required
to affect the inspection. Clean and prepare 9000-4 splice plates
spanning the spar flange notches and adjacent areas of the spar for
close visual inspection.
(4). Visually inspect all (22) fasteners
attaching the 9000-4 splice plates to the 9000-3 front spar for
condition and security. The fasteners should not be bent, nicked,
cracked, or corroded, and should be tight. Remove any suspected
fasteners.
(5) Visually inspect the splice plates, the
lower 7.5 inches of the spar flanges and the spar web for cracks.
(6) Dye-penetrant inspect both sides of the
spar web, the side flange bend radii (fillets) and the side flanges of
the 9000-3 spar 2.0 inches above and below the bend on both sides for
cracks. Verify crack indications (inside and outside this area) that
were discovered in the visual inspections. Extend the dye-penetrant
inspection area as indicated by findings. This inspection must be
accomplished using the instructions accompanying the dye-penetrant
inspection equipment. Use AC 43.13-1B Chapter 5, Section 5 for guidance
and ASTM E-1417 as appropriate.
(7). Remediate damage:
i. Blend out minor damage indications
(cracks, scratches, corrosion) using hand tools and sandpaper as
appropriate to eliminate, verify that remaining indications are
cracks.
ii. If a crack is (cracks are) found in the
flat areas (away from flange bend radii), then mark the visual end(s)
of the crack(s).
1. If the marked crack length is less than
or equal to 0.125 inch, then profile notch out the crack (0.0625 min
R) or drill out the crack using a #30 (0.1285 inch) drill.
2. If the marked crack is greater than
0.125 inch but less than or equal to 0.250 inch, then stop drill
(each end) using a #30 (0.1285 inch) drill, ensuring that the drill
hole(s) does (do) not ride into the flange bend radius and that the
crack does not extend beyond the stop drill hole(s). Machine out the
ligament between the stop drills or to the nearby edge. The notch
edges need not be parallel, but should be smooth simulating a
V-notch or elliptical hole.
3. If the marked crack is greater than
0.250 inch, then stop drill (each end) using a #30 (0.1285 inch)
drill ensuring that the drilled hole(s) does (do) not ride into the
flange bend radius and the crack does not extend beyond the stop
drill hole(s).
iii. If the crack extends entirely across the
spar (as in Figures 2 and 3), then remove fasteners so as to separate
the parts. Deburr and smooth the crack edges as much as possible
without affecting the fit. Retain the parts for re-installation.
iv. If a crack is (cracks are) found in the
flange (fillet) radius (radii), the machine out the crack so as to
remove the entire radius (0.19 inch minimum on web and flange) using
0.06R min corner radii in the slot and straight across the fillet at
the ends. Optionally, stop drills may be used if they are carefully
blended so as not to adversely interact with the bend radius.
v. Clean all parts removing dye-penetrant
chemicals in accordance with instructions accompanying the dye-penetrant
equipment. Use AC 43.13-1B Chapter 5, Section 5 for guidance and ASTM
E-1417 as appropriate and allow to dry.
vi. Coat all newly exposed surfaces with zinc
chromate or zinc oxide in accordance with standard repair facility
practices. Use AC -13-1B Chapter 6, paragraph 6-40 as a guide. Restore
finishes.
(8). If damage was found in the visual or dye-penetrant
inspections, then fabricate and install a web repair doubler as
described below. If damage is not found, then fabricate and install the
repair doubler described below as a preventative modification
(alteration).
(9) Fabrication of Repair or Alteration Doubler
i. Fabricate a repair (or alteration) doubler
from 0.090 2024-T3 (clad) aluminum alloy as sketched in Figure 10. Use
1AC 43.13-1B Chapter 4, Section 4 and Chapter 6 for guidance.
Figure 10
ii. Blend the chamfer run-out at intersection
with the upper (left Figure 10) profile. Custom fit the doubler to the
aft face of the 9000-3 front spar adjusting the bend angle, position
and chamfers as required. Coat with zinc chromate or zinc oxide per AC
43.13-1B Chapter 6, paragraph 6-40, and allow to dry.
(10) Repair or Alteration Doubler Installation
i. If the 9000-4 splice straps were removed,
then clean up the holes and re-install them using existing holes in
the spar cap as the template to locate the splice straps, and using
the same size and type of fasteners (AN470-AD4 rivets) as were
removed. If the holes were severely damaged, then drill for and use
the next size AN470-AD5 rivet or equivalent. If the spar was severed
and the lower section was removed for refurbishment, then install the
fasteners above the break first to locate the straps, then install the
fasteners below the break using the existing 9000-4 strap as a
template.
d. Install the repair/modification doubler
onto the 9000-3 front spar:
i. Position the repair/modification doubler
onto the aft face of the 9000-3 spar web as it was custom fit during
the fabrication process.
ii. Clamp the doubler in place. Using the
9000-3 web holes (below the spar bend) as a template, carefully
match drill at least three holes in the doubler and temporarily
install at least three AN3-X bolts to locate the doubler, where X is
the appropriate grip length for the stack-up including washers under
the nut as required.
iii. Using the 0.090 doubler holes as
template, drill 0.190 holes in the 9000-3 web and install 7 AN3-X
Bolts (or equivalent) using MS21042-3 Nuts and NAS620-10 Washers
under the nut (or equivalent), where X is the appropriate grip
length for the stack-up including washers as required. Use AC
43.13-1B Chapter 7 for guidance. If not already done, match drill
the remaining holes below the spar bend. Remove the temporary
fasteners. Remove the clamp.
(11) If the 8000-37 clip was not removed
during the disassembly, remove it by carefully drilling out the
rivets. Use AC 43.13-1B, paragraph 4-52.b for guidance. Fabricate a
new 8000-37 Clip from 2.13 x 2.0 x 0.040 2024-T3 (clad) aluminum
alloy. Use AC 43.13-1B Chapter 4, Section 3 paragraph 4-38b, Section 4
paragraphs 4-53 and 4-55 and Chapter 8 for guidance. Use the existing
8000-37 Clip as a template for sizing and for the bend angle, but do
not mark or drill the fastener holes until assembly.
(12) Reinstall Removed Structure
Note: Installation procedures are
described in the Varga Kachina 2150A Aircraft Maintenance Manual
Section 4.4.4.2, 4.4.3.2, 4.4.2.2 and 4.4.1.2 which may be used to
supplement the following instructions.
a. Install the Vertical Stabilizer:
i. Install a new seal extrusion (or
re-install the old if it is in excellent condition) on the skin
lower edges.
ii. Existing hardware may be reused if it
is in excellent condition except self-locking nuts and cotter pins
must be replaced.
iii. It may be necessary to remove some of
the tongue at the u-shaped slot in the 8000-69 skin (Figure 9)
accommodating the 9000-3 front spar in order to clear the spar/doubler
assembly. Try to maintain 0.190 inch minimum edge distance from
existing holes, but shorter edge distance is permissible. Coat newly
exposed material with zinc chromate or zinc oxide using repair
facility standard procedures, and allow to dry. Use AC 43.13-1B
Chapter 6, paragraph 6-40 for guidance.
iv. Carefully fit the vertical stabilizer
into position so that existing holes in the front and rear spars
align with the corresponding holes in the bulkheads.
v. Use tapered drifts and/or vertical
stabilizer supports to ensure 100% alignment. Support the tail in
position.
vi. An optional tapered shim may have been
installed at the FS 193.06 bulkhead to maintain vertical tail
incidence (Figure 9). If the shim was installed, re-install the
existing one, or if it was damaged in tail removal, fabricate a new
one using the existing one as a template and position it as
required. If a new shim is installed, drill the shim to match the
existing hole pattern only after the vertical tail is properly
positioned and the shim is snug.
vii. Locate and mark the new 8000-37 clip
to match existing holes in the 8000-69 fuselage skin and rivet in
place. This may be done in several ways. Suggested methods include
using inked cotton balls stuffed into the existing holes as markers,
or "bluing" the surface, or removing the tail sufficiently
to gain access to the clip holes (if tail is completely removed, a
temporary 0.154 inch shim may be temporarily used to simulate the
spar/doubler stack-up to locate the forward face of the clip,
include the tapered shim if used). If the tail is sufficiently
removed, three AN470-AD4 rivets may be used. Cherry rivets or
equivalent "blind fasteners" may be optionally used. New
holes located aft or forward of the existing holes in the 8000-69
skin tongue may be used. Be careful of dimensions so as to ensure
positive engagement of the fasteners. While short edge distance or
close hole spacing is permitted, exercise care so as to affect a
secure attachment.
viii. Reinstall or recheck the alignment of
all fasteners holes in the front and rear spar using tapered drifts
and/or vertical stabilizer supports as required.
ix. Install all NAS 1103 bolts attaching
the rear spar to the FS 206.38 bulkhead and the 8000-8 horizontal
bulkhead using new hardware of the same type and size as was
removed. Note that the bolts are different lengths. Install snug
(not torqued). If the spar or bulkhead holes were damaged so as to
require clean-up, then if resulting hole is less than 0.196 and
adjacent holes are nominal size (0.189 inch for NAS 1103, or similar
fit for oversized bolts) then install NAS1103 or equivalent. Else,
drilling for and installing NAS1104 bolts (or up to one size over
the size removed at individual locations as applicable) is
permissible.
x. Using the FS 193.06 bulkhead (and spar
web) holes as a template, drill the top 3 holes through the 8000-37
clip. Install the NAS 1103-X bolts (12 bolts) attaching the front
spar to the FS 193.06 bulkhead (through the tapered shim if
installed) using new bolts (0.090 longer grip than those removed) if
required plus nuts and washers of the same type and size as were
removed.
xi. Install all fasteners snug (Varga
Maintenance Manual Figure 4.14, reproduced here as Figure 9, may be
used for guidance), then torque nuts for (including front spar and
rear spar attachments). Use Varga Maintenance Manual Table II.II
(Figure 11) for guidance:
Figure 11
b. Install the Rudder
i. Installation is opposite of removal.
Install rudder hinge pins snug, but do not overly pinch clevises
(Figure 12). Use new cotter pins.
ii. Reattach the rudder control cables
(Figure 7).
iii. Install Rudder Hinge and Rudder Cable
Bolts snug, but do not overly pinch the clevises or shackle. Use new
cotter pins.
iv. If the rudder balance weight was
removed, reinstallation is opposite of removal (Figure 7). Torque
nuts using Varga Maintenance Manual Table II.II (Figure 11) for
guidance.
v. Reinstall the vertical stabilizer tip.
Installation is opposite of removal.
vi. Inspect the rudder for operation and
travel after installation, that there is no binding or misrouting of
the cables in the fairleads or pulleys (Figure 7), and that rudder
pedal springs are providing tension. Rudder should move freely 29º
±1º each way. Adjust control stops on the FS 206.38 bulkhead as
required. The Varga Maintenance Manual Figure 5.6 and 5.7 (Figure
13) provides instructions for making a template and adjusting the
stops. Note that some models have double nuts and some have nut
plates for the stop screws.
Figure 12
Figure 13 a
Figure 13b
c. Install the Horizontal Stabilizer
i. Installation is opposite of removal
(Figure 8). Ensure that fixed surface spacers are in place prior to
installing the bolts.
ii. Torque nuts using the Varga Maintenance
Manual Table II.II (Figure 11) for guidance.
iii. Install new cotter pins.
d. Install the Elevator
i. Whether the elevator was removed from
the horizontal stabilizer during disassembly or not, perform the
relevant steps below.
ii. Installation is opposite of removal.
iii. Install new cotter pins.
iv. Reinstall the elevator static balance
weights to the elevator bell-crank (Figure 6). Torque nuts using the
Varga Maintenance Manual Table II.II (Figure 11) for guidance.
v. Reattach the elevator control tube and
Elevator Trim Control Tube to the elevator horn (Figure 6). Install
bolts snug, but do not overly pinch clevises. Use new cotter pins.
vi. Reinstall the Tail Cone. Installation
is opposite of removal.
vii. When re-attaching the tail light wire
knife splice use a new clear vinyl insulating sleeve tied-off on
each end using waxed chord secured with a square knot (Figure 5).
viii. If the tail light wire was cut during
removal, then slip a clear vinyl sleeve onto one end and splice
using either a crimped splice or a knife splice similar to the
existing knife splice – protect with a clear vinyl sleeve tied off
on each end with waxed chord secured with a square knot (Figure 5).
If sufficient slack is not available to affect the splice, then
replace one section with wire of the same size and type and
crimp-splice and protect in two places as described above – retain
at least one knife splice as in the original configuration.
ix. Verify that elevator travel is free
between 16º±1º up and 18º±1º down. Adjust control stops on the
forward and aft control sticks as required (Figure 14, items 11 and
12). For elevator rigging, at neutral the Bellcrank at FS 158.0 and
the forward stick should be vertical and the elevator should be in
its static balance condition so that the elevator upper surface
(forward-to-aft) is 2.5° ± 1° below a horizontal datum.
x. Verify tail light operation.
Trouble-shoot and re-splice as required.
Figure 14
e. Reconnect the VOR Antenna coax cable if
installed. If the cable was cut during removal of the vertical
stabilizer, then repair upon using a matched set of BNC cable
connectors using procedures accompanying the connectors. Verify
proper VOR operation. Troubleshoot and re-splice as required.
f. Recheck that all fasteners are properly
torqued, that all cotter pins are installed and that safety wires
are used as applicable. Reinstall the fuselage side access panel.
g. Reinstall the access panel on the
fuselage side panel (Figure 4 Item 17).
Home
|